Produce hydrogen-based directly reduced iron (HDRI) in an EAF
key word:HRDI, hydrogen reduction, iron
Source: internal company

Against the background of “carbon peak” and “carbon neutrality” in China, the traditional and long process of using a blast furnace converter in the steel industry is limited by many problems (such as limitations related to resources, energy, and the environment), and the carbon reduction potential of this process is also limited. The electric arc furnace (EAF) steelmaking process has the advantages of a shorter duration, recyclable resources, and low energy consumption, and the amount of carbon emissions of per ton of steel is far lower than that of the aforementioned longer process. At present, short-process EAF steelmaking involves scrap steel as its main raw material; this is an important aspect of manufacturing in the steel cycle. However, in the recycling process of scrap steel, there are problems such as uncontrollable mass composition and enrichment of impure elements, which will inevitably affect the quality of steel materials. The direct reduction of iron based on hydrogen reduction has the benefits of low carbon emissions, stable composition, and low contents of impurities; it produces high-quality raw materials for the subsequent production of high-quality steel. The new process of producing hydrogen-based directly reduced iron (HDRI) in an EAF will be important for the future production of high-quality steel.
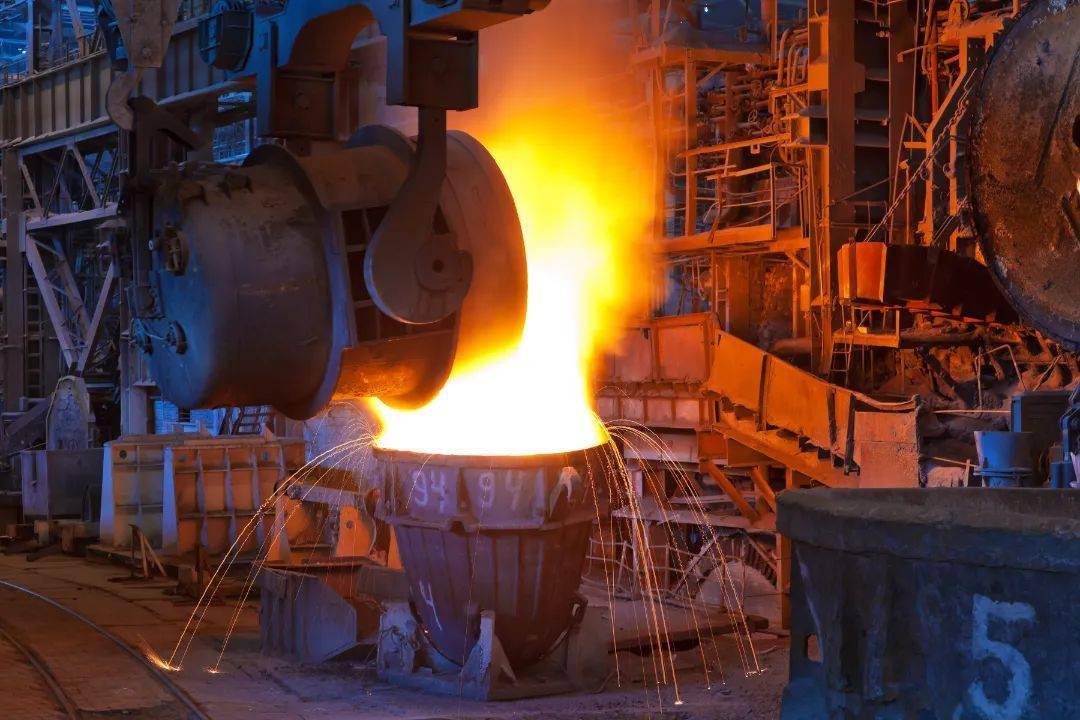
Hydrogen-based directly reduced iron (HDRI) is produced by reducing iron ore with pure hydrogen in a gas-based shaft furnace, where hydrogen constitutes more than 55% of the reacting gas. By January 17, 2024, CISRI had independently developed and built the world's first HDRI demonstration project in Linyi, Shandong, which operated for 300 hours and achieved an HDRI metallization rate exceeding 93%. HDRI serves as a raw material for high-purity iron or high-end special steel and is melted or smelted in an electric furnace.
Currently, electric furnaces often use directly reduced iron (DRI) and some scrap steel for smelting. The melting of solid materials, especially HDRI, is crucial in optimizing the smelting process. HDRI differs from scrap steel in several ways: it has low carbon content, a uniform shape and composition (typically 10-16 mm balls), a dense pore structure, lower density, and a melting point lower than the melting tank temperature. As a result, the melting process of HDRI is mainly controlled by heat transfer, and the influence of the carburizing process is not significant.
While the production of HDRI reduced by pure hydrogen gas is minimal, DRI obtained via direct reduction using CO and hydrogen gas has been utilized and shares similar characteristics with HDRI. The melting of DRI in an electric furnace relies on heating from the arc of the liquid steel melting tank and stirring. Poor melting of DRI can lead to the "iceberg" phenomenon, affecting the smooth progress of electric furnace smelting.
Previous studies have focused on the macroscopic influence of DRI on electric furnace smelting, with limited research on the melting process of low-carbon HDRI obtained through direct reduction using hydrogen or hydrogen-rich gas. Therefore, there is an urgent need for reasonable methods to study the melting process and bonding phenomenon of HDRI in an electric furnace melting pool.