Briquette Machineis one of the main equipment for powder and granular material forming technology, and has a wide range of industrial applications. Ball pressing is usually used as a part of the manufacturing process, possibly to reduce the need for dust removal and ventilation. Sometimes, its ball pressing products can also be sold as end products.
For high-pressure ball presses, we usually consider a line specific pressure of (5-12) t/cm as the high-pressure ball press, and commonly used ones are: 80KN/cm; 110KN/cm; 120KN/cm; 150KN/cm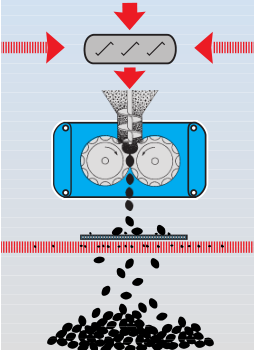
Principle of Ball Pressure:
The powdered material is compressed and formed between a pair of rotating pressure rollers, one of which is movable and provides pressure through a hydraulic system. The surface of the pressure roller has a customized mold. The material may be a single or mixed material, or it may require the addition of a certain binder. (As shown in the figure on the right)
Equipment selection:
1. Line pressure ratio: refers to the pressure per unit pressure stroke width, unit: t/cm or KN/mm. Usually determined by pressure ball experiments, reliable data is also available in practice for typical materials.
2. Preliminary selection of roller diameter and width based on production capacity requirements. Note: Different ball shapes have a significant impact on production capacity.
3. It is usually provided by the end user and optimized by the device manufacturer before being determined. Determine the model based on line pressure ratio, spherical size, and processing capacity.
Process flow:
The ball forming performance of different materials varies, and the selection of ball pressing machine and process is also different. In addition, the requirements for the end product are also important factors determining the process.
The balling performance of materials depends on the material itself, such as fineness, particle size, moisture content, composition, etc., which usually require testing to determine.
Not all materials have sphericity. If the bonding force between particles is low, a suitable adhesive is necessary. According to the physical properties of the material and the purpose of forming the ball, the selection of adhesive needs to be based on its bonding performance and usage cost. Various (liquid or solid) adhesives such as starch, bentonite, asphalt, quicklime, cement, water, flour, lignosulfonates, molasses, polymers, resins, sodium silicate, and new composite adhesives for specific purposes.
The key process of ball pressing equipment is "continuous quantification", so continuous batching, mixing, and subsequent drying steps are usually required in the process (see sample booklet for details on batching and mixing steps)
In practice, Kaizheng Company has accumulated considerable experience and possesses complete turnkey system capabilities (including electrical interlocking and interface control). The integrated system forming unit is used to meet your specific needs.
Note: (The process may vary depending on the material and usage).
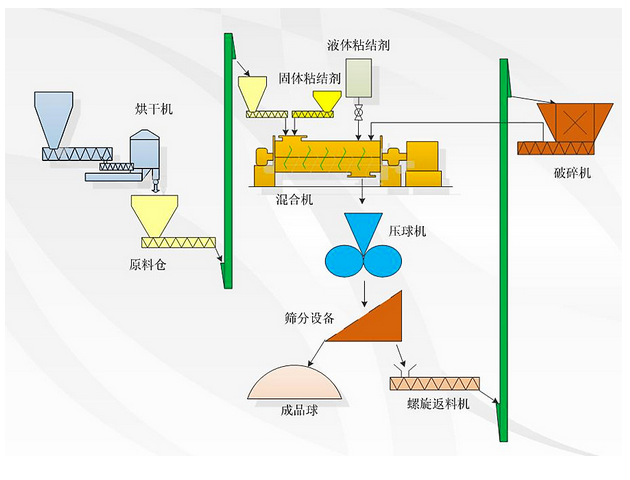
Main features:
1. The transmission system adopts: motor - elastic coupling (belt drive) - double output shaft reducer - gear coupling - one or two pressure rollers;
2. Assembly forms of pressure rollers: three types of structures: hot installation structure, detachable expansion sleeve, and segmented roller sleeve embedding structure.
3. Material of pressure roller: high-quality bearing steel, cold work mold steel martensitic stainless steel (suitable for acidic materials)
4. Bearing assembly: equipped with a pull-out sleeve structure and special tools for disassembly and assembly
5. Pre compression spiral: one of the core technologies. Specially designed according to the characteristics of the material (mainly referring to fluidity, abrasiveness, particle size), with cleaning and extrusion functions. Design variable pitch spiral for particularly difficult to form materials
Application materials:
1. Minerals: bauxite, limestone, aluminum ash, dolomite, gypsum, clay, magnesium oxide, fluorite, pigments, laterite nickel ore, vanadium pentoxide, zirconium hydroxide, zircon sand
2. Metal minerals: chromium nickel iron, metal manganese powder, silicon manganese alloy, molybdenum oxide, chromite powder, manganese ore powder, chromium iron, nickel iron
3. Directly reduce iron cold pressed blocks.
4.Various types of dust removal ash (electric furnace dust removal ash, converter dust removal ash, blast furnace dust removal ash, sintering powder, coke powder...)
5. Coal, carbon black, graphite, charcoal
6. Iron coke, carbon containing pellets
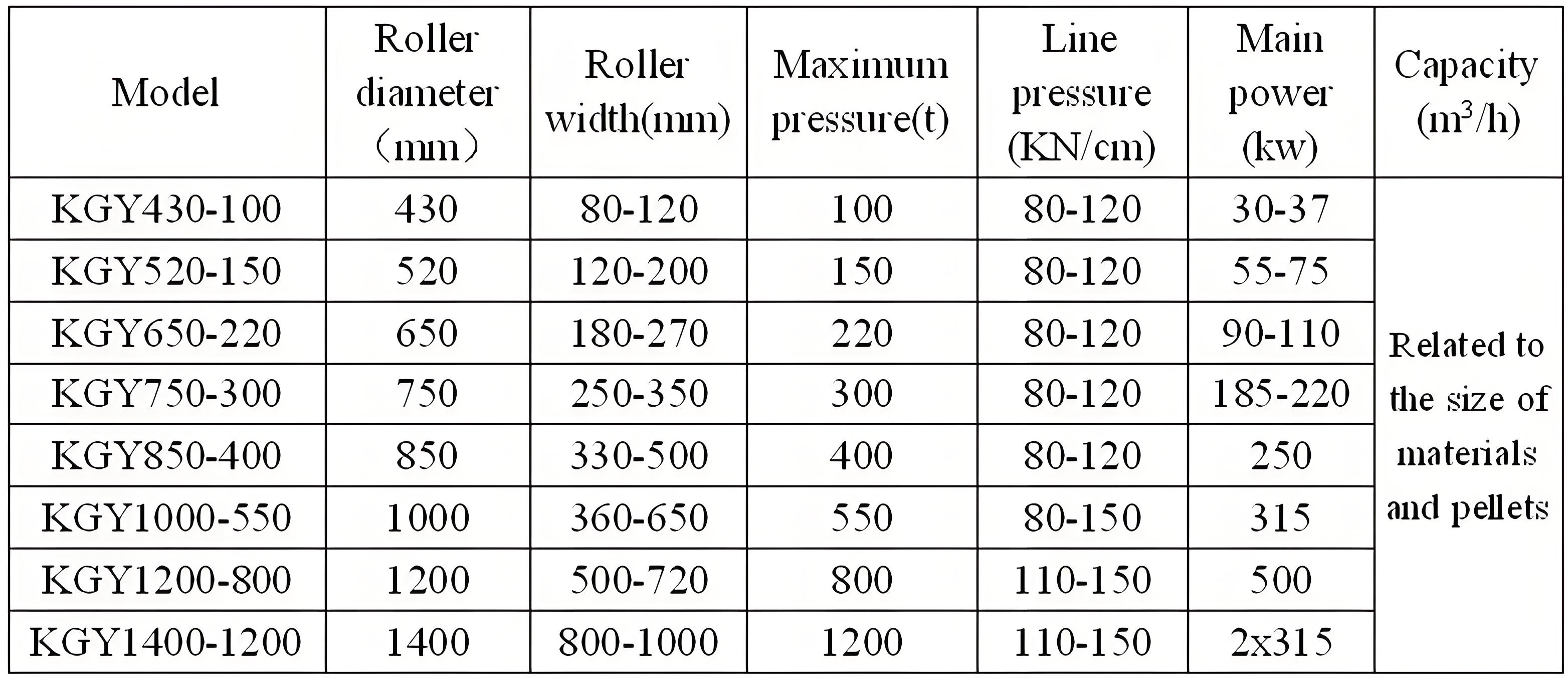
